These are major mistakes commonly found after constructing homes or buildings.

Narrow space in the
toilet.

Can't open both doors at the same time.

Unusable area.
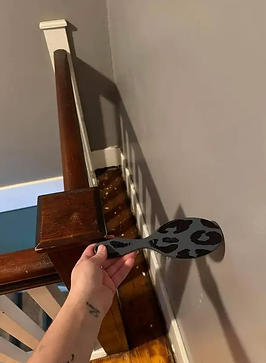
Narrow, unusable space.

The cooktop and upper cupboard are misaligned.

Narrow, unusable space.

Narrow, unusable space.
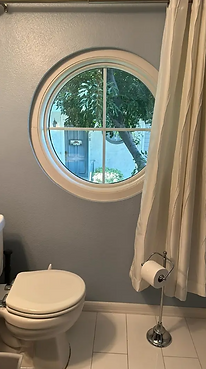
Can't stand pee.The window level is too low.

Incorrect steps merged.

Incorrect room doors.

Narrow space in the
bed room.

Shower water flows toward the toilet.

Limited space for toilet installation.

Impossible to open the
door fully.
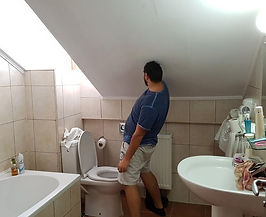
Difficult to stand while peeing.
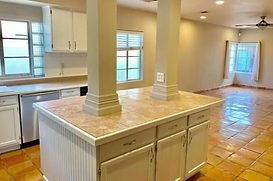
The column stands on
the table.
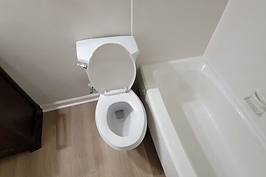
Unable to sit on the toilet
due to narrow space.
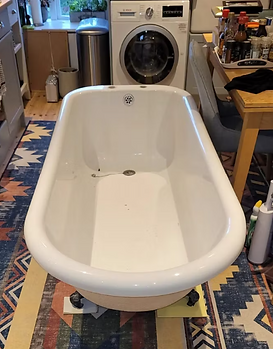
Unable to open the washing machine door.

There is no space for the refrigerator.

Unable to open the drawers.

Unable to close the door.
Avoid the above mistakes when building your dream house.
We have the solution.
The 3D printed scale model accurately displays the actual sizes, making it easy to identify errors before construction. It also allows customers to visualize how the interior will look.
Anyone can generate an image of their dream home before it's built, allowing them to visualize the spacing and interior layout easily.

We build custom residential and factory 3D models and 3D printing.
All 3D-printed items in the picture below are 1:50 scale.
Your clients will be impressed when you present them with a 3D-printed scale model of their new home or building!
3D Residential Models and Technology

Visualizing realistic 3D representations from 2D home design images and text descriptions can be challenging for those outside the industry. However, 3D printers now provide an affordable and efficient way to create detailed residential models, making it easier to showcase ideas and plans to homebuyers, city planners, investors, and planning commissions. With these models, investors and potential buyers no longer need to decipher complex AutoCAD printouts to understand and visualize their potential investments.
3D printing is a rapidly evolving technology with boundless potential. Modern advancements in printing technology now enable the creation of highly accurate home designs, delivering intricate details with remarkable precision—all at a cost-effective price.
Residential models of single-family homes, apartment complexes, and townhomes are beneficial in the planning, design, construction, marketing, and sales process of residential home planning.
on almost every site.
What are the advantages if we make room interior 3D model before make a house?
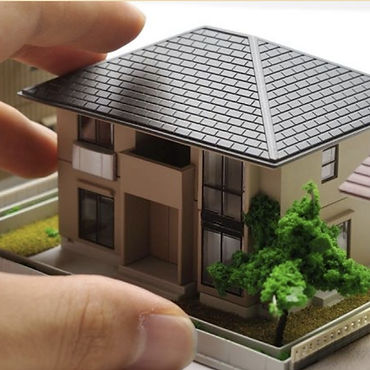
Better Visualization
• Helps you see how the space will look before construction begins.
• Allows you to experiment with different layouts, colors, furniture, and lighting in a realistic way.
•Avoids surprises by giving a clear picture of the final outcome.

Efficient Space Planning
• Ensures rooms are functional and practical for daily use.
• Helps in optimizing furniture placement and space utilization.
• Identifies potential issues like tight spaces or inefficient layouts early on.

Cost Savings
• Reducing waste of materials by ensuring accurate measurements and
planning.
• Helps avoid costly modifications during or after construction.
• Prevents unnecessary purchases of furniture, decor, or materials
that don’t fit well.

Error Detection & Problem Solving
• Detects design flaws like awkward room proportions or poor lighting arrangements before construction.
• Identifies electrical and plumbing issues, ensuring proper outlet and fixture placement.
• Ensure that doors, windows, and furniture fit properly in the design.
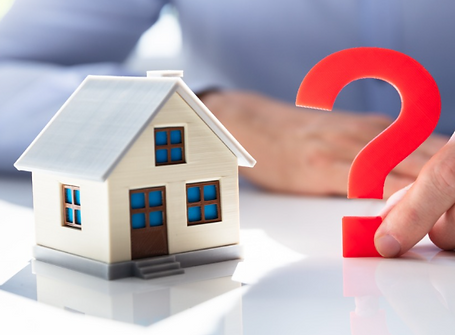
Faster Decision-Making
• Makes it easier to choose wall colors, flooring, lighting, and furniture styles.
• Allows for quick changes in the design stage instead of making changes
during construction.
• Provides a realistic preview for homeowners and builders, reducing confusion.
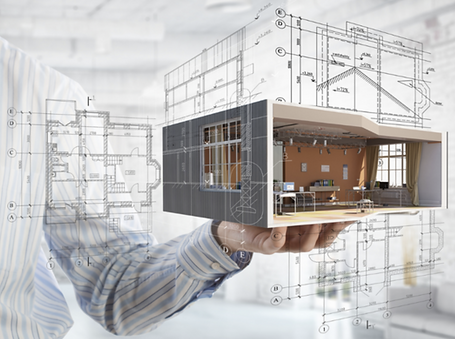
Improved Communication with Contractors
• Helps architects, interior designers, and builders understand the exact vision.
•Reduces misunderstandings by providing detailed 3D views instead of relying only on 2D drawings.
• Allows for easy collaboration and adjustments before starting construction.
How do 3D printed models help clients?

The client cannot understand 2D drawings, but the 3D printed model makes it easy to visualize and capture the design.

With 3D-printed model homes, clients can easily visualize the shape and gain a clear understanding of the interior space before making a purchase.

With a 3D-printed factory layout, clients can easily identify pipe clashes, gain a clear understanding of space and scaling, visualize the design effectively, and keep a physical record for future reference.
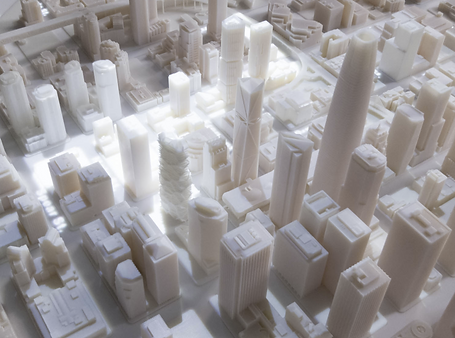
A 3D-printed architectural village model enhances visualization, improves spatial understanding, and aids early design validation. It facilitates communication, serves as a marketing tool, supports urban planning, and acts as a long-term reference for future modifications and education.

A 3D-printed factory structure model enhances visualization, improves spatial understanding, and helps detect design issues early. It aids communication with stakeholders, optimizes workflow, and supports process planning. The model also attracts investors and serves as a reference for future expansions and training.

A 3D-printed factory pipeline model improves visualization, aids in design and planning, and detects issues early. It enhances coordination, streamlines maintenance, saves costs, and serves as a training tool and future reference
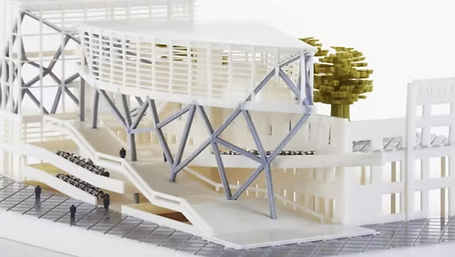
A 3D-printed architecture model improves visualization, aids in design evaluation, and helps identify issues early. It enhances communication, speeds up decision-making, serves as a marketing tool, and reduces costs by minimizing revisions.
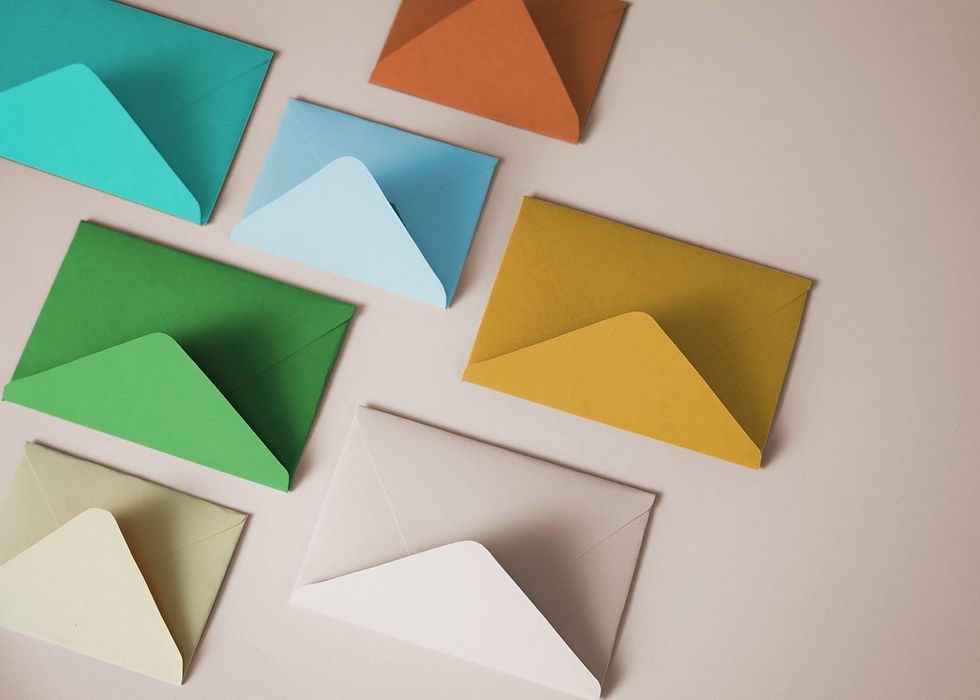